Key Components of PVC Pipe Extrusion Machinery:
1.Belt Loader: it is responsible for transporting plastic film waste into the agglomeration hopper, it ensures a continuous and controlled feed of material into the line.
2.Agglomerate Extruder Machine: The machine first shreds large plastic films into smaller fragments, making them easier to handle and process, then the smaller fragments are compressed and rolled into dense, irregularly shaped agglomerates under friction-generated heat or external heating systems. The extruder features a screw mechanism that conveys the material through a heated barrel, where it is melted and mixed. The design allows for precise temperature control and material mixing.
3.Screen Changer: it is to remove impurities, such as dirt, dust, and degraded material, from the molten plastic. This ensures that the final product has a consistent quality and meets the required specifications. The double station design allows for continuous operation of the extrusion process, while one screen is in use for filtering the molten plastic, the other screen can be cleaned or replaced without interrupting the flow of material.
4.Extrusion Mold: shape the melted plastic into a continuous strand as it exits the extruder. This is a critical step in forming the material into a pelletizable form.
5.Horizontal Head Die Cutting and Cooling System: This component cuts the extruded strands into pellets of desired size. The horizontal design allows for efficient cutting and handling of the material. This system typically involves a water bath that cools the freshly cut pellets, preventing them from sticking together and ensuring they are ready for further processing.
6.Dewaterer: The dewaterer removes excess moisture from the cooled pellets, ensuring they are dry and suitable for storage or further processing. This machine often uses centrifugal force to separate water from the pellets, enhancing the quality of the final product.
7.Air Feeding Storage Soil: This system is responsible for transporting the dried pellets to storage silos or bags for easy handling and distribution.
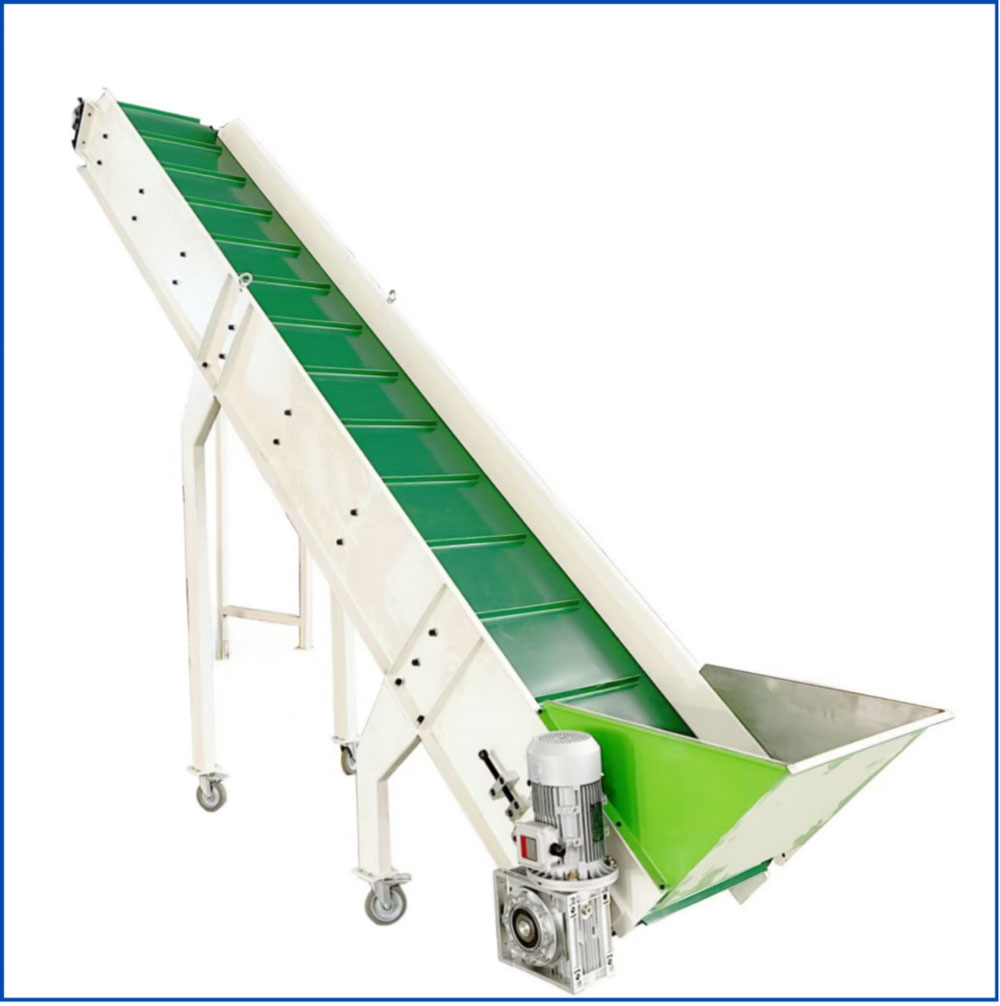
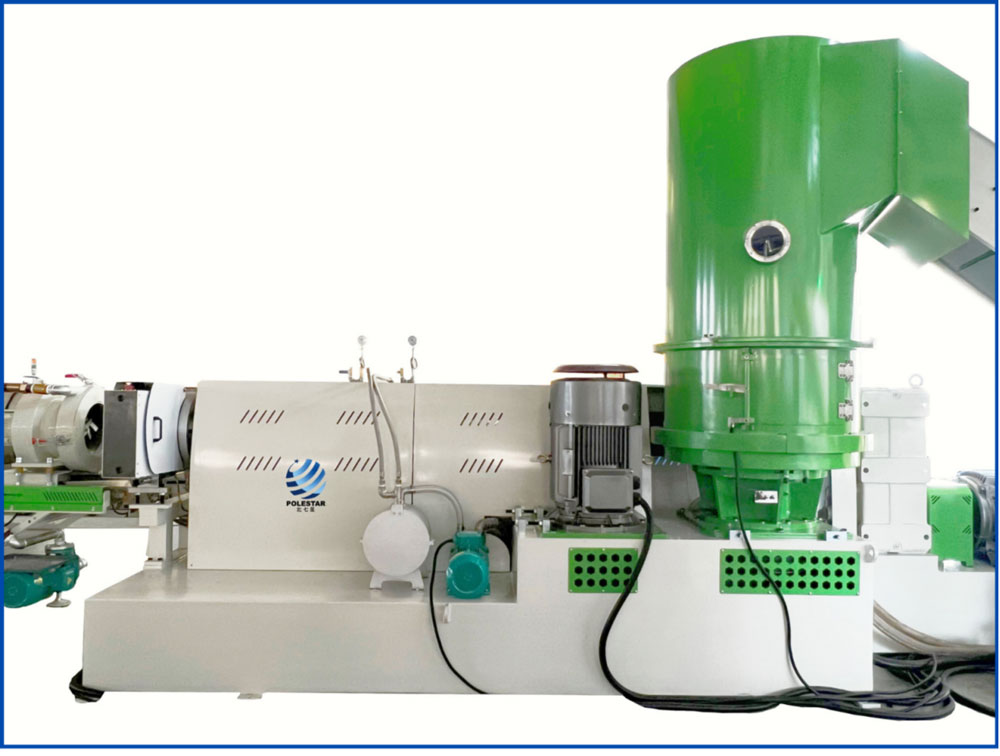
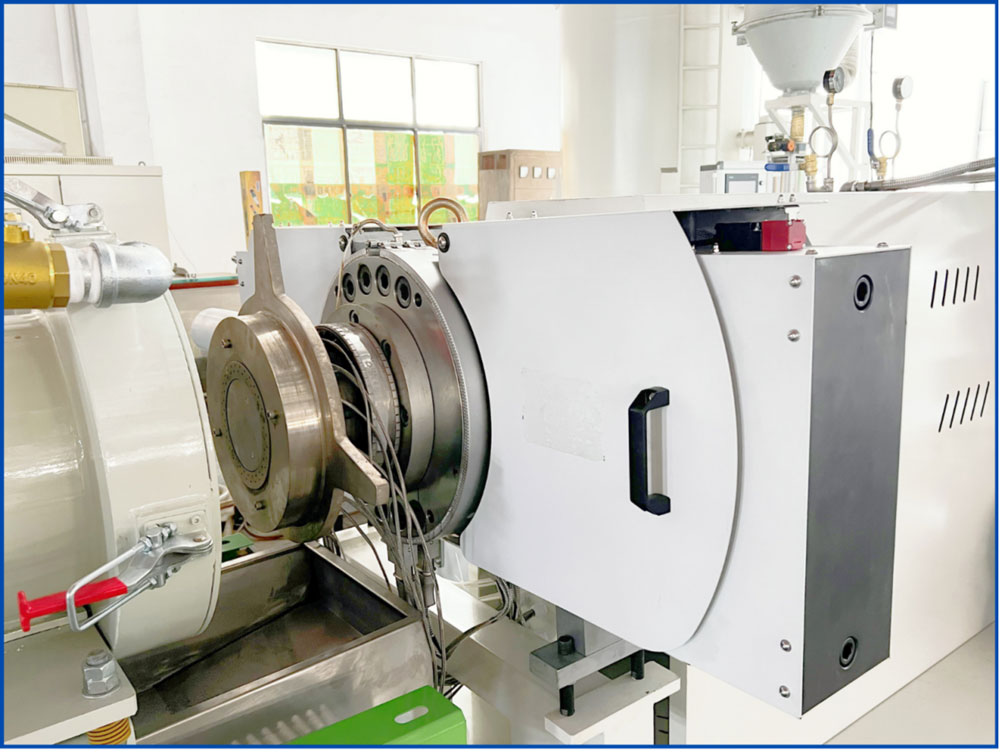
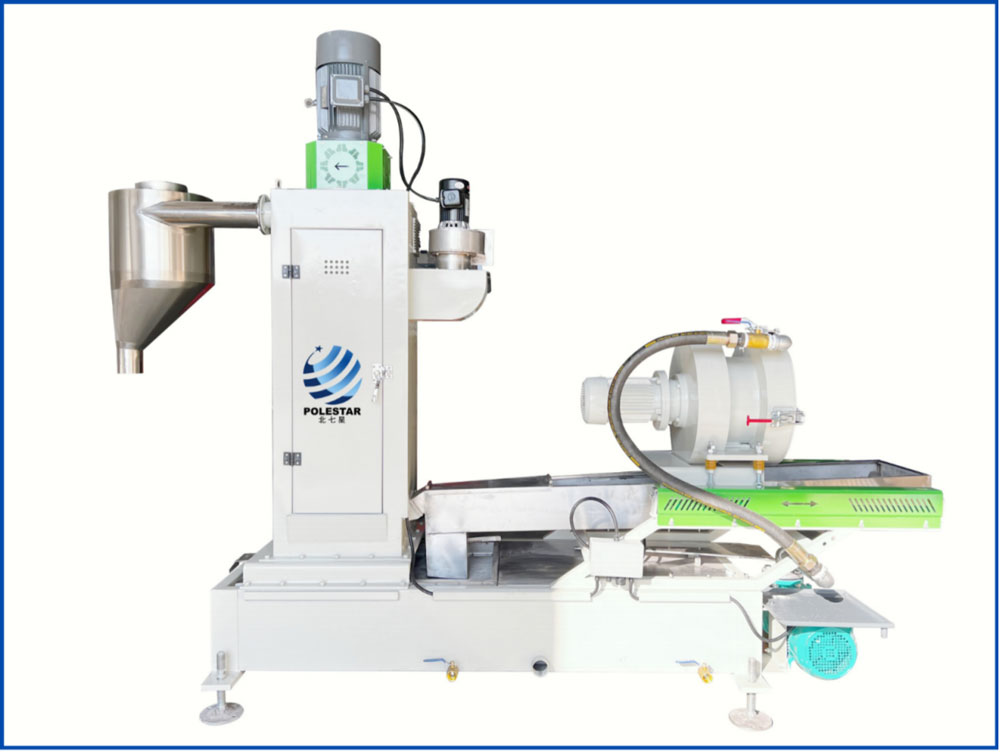
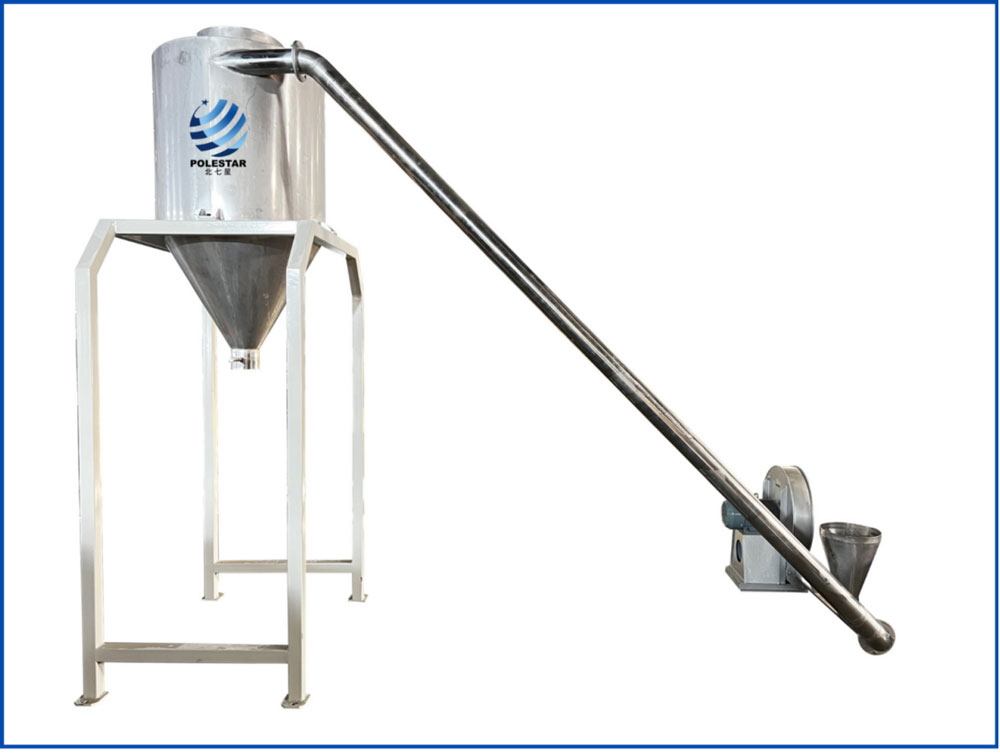
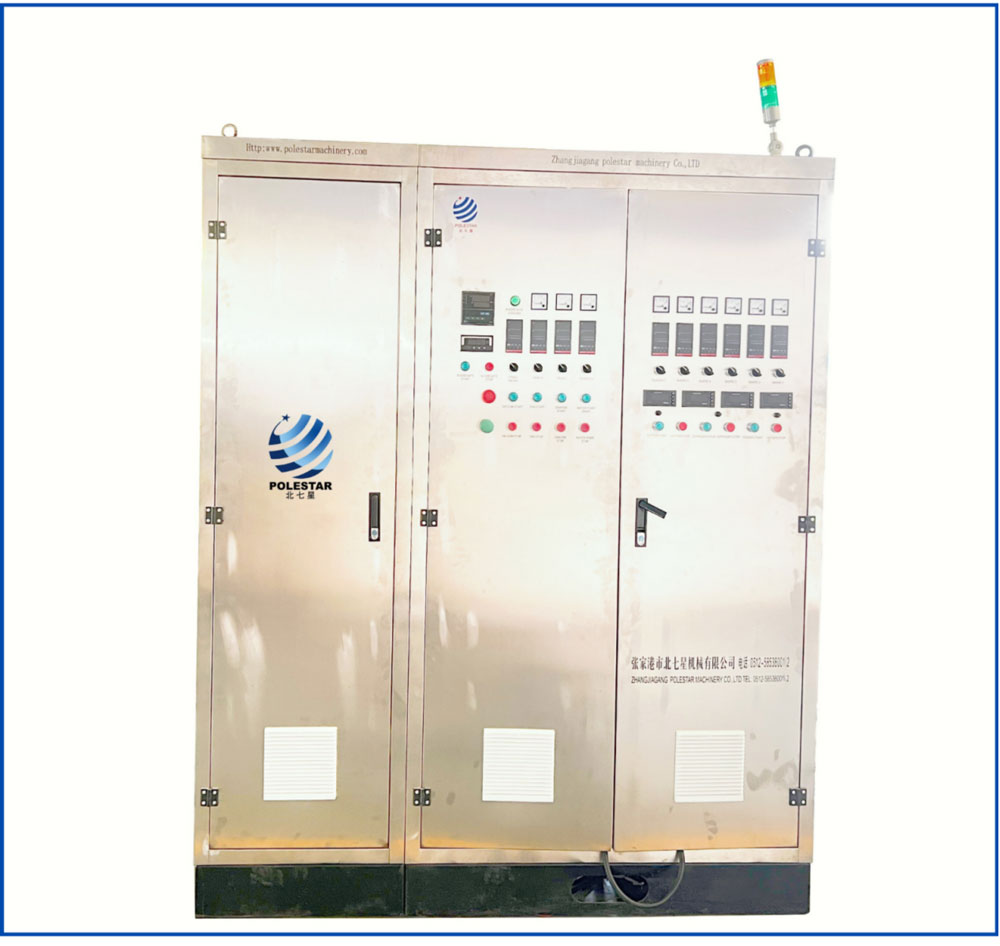