Double-Head Extrusion Line For PVC Pipe From 20 To 63 mm
播放视频
Description
This double output PVC pipe extrusion line designed for producing pipes with diameters ranging from 20 to 63 mm. This type of extrusion line is capable of producing two pipes simultaneously, which enhances productivity and efficiency. Here’s an overview of its key components and features:
Key Components of PVC Pipe Extrusion Machinery
1. SJZ55/110 Conical Twin-screw Extruder:
It is a highly efficient and versatile machine that plays a crucial role in the PVC pipe processing industry.
- Feeding System: The feeding system is designed to ensure a consistent and uniform feed of raw materials into the extruder. It may include a hopper and a gravimetric or volumetric feeder.
- Conical Design: The screws are arranged in a conical shape, which allows for better mixing and melting of the material. This design helps in achieving a more uniform melt and improved material processing.
- Twin-Screw Configuration: The twin-screw design consists of two intermeshing screws that rotate in the opposite directions. This configuration enhances the mixing and conveying of materials, leading to better product quality.
- Barrel: The barrel houses the screws and is equipped with heating and cooling zones to control the temperature during processing.
- Control System: a sophisticated control panel allows operators to monitor and adjust parameters such as temperature, pressure, and screw speed, ensuring optimal processing conditions.
2. Die Head:
- A specially designed die head that allows for the simultaneous extrusion of two pipes.
- The die can be adjusted to produce pipes of varying diameters within the specified range (20 to 63 mm).
3. Vacuum Calibration and Cooling Tank:
- After exiting the die, the pipes are calibrated to ensure they meet the required dimensions.
- A cooling system, often using water, helps solidify the pipes and maintain their shape.
4. Haul-off Machine & Cutting Machine:
- This haul-off unit pulls the extruded pipes at a controlled speed to ensure consistent length and quality. It may include multiple caterpillar-type grips to handle two pipes simultaneously.
- Cutting machine help accurately cuts the pipes to the desired lengths. It can be synchronized with the haul-off unit for precise cutting.
5. Control System:
- An advanced control panel that allows operators to monitor and adjust parameters such as temperature, speed, and pressure.
- It may include PLC (Programmable Logic Controller) technology for automation and efficiency.
Parameters
Production Line Flow Chart
Raw material+additive → Screw Loader → Screw Feeder → Twin-screw Conical extruder → Double-head Extrusion die → Vacuum calibration tank → Haul-off & Cutting machine → Stacker
The production line consists of
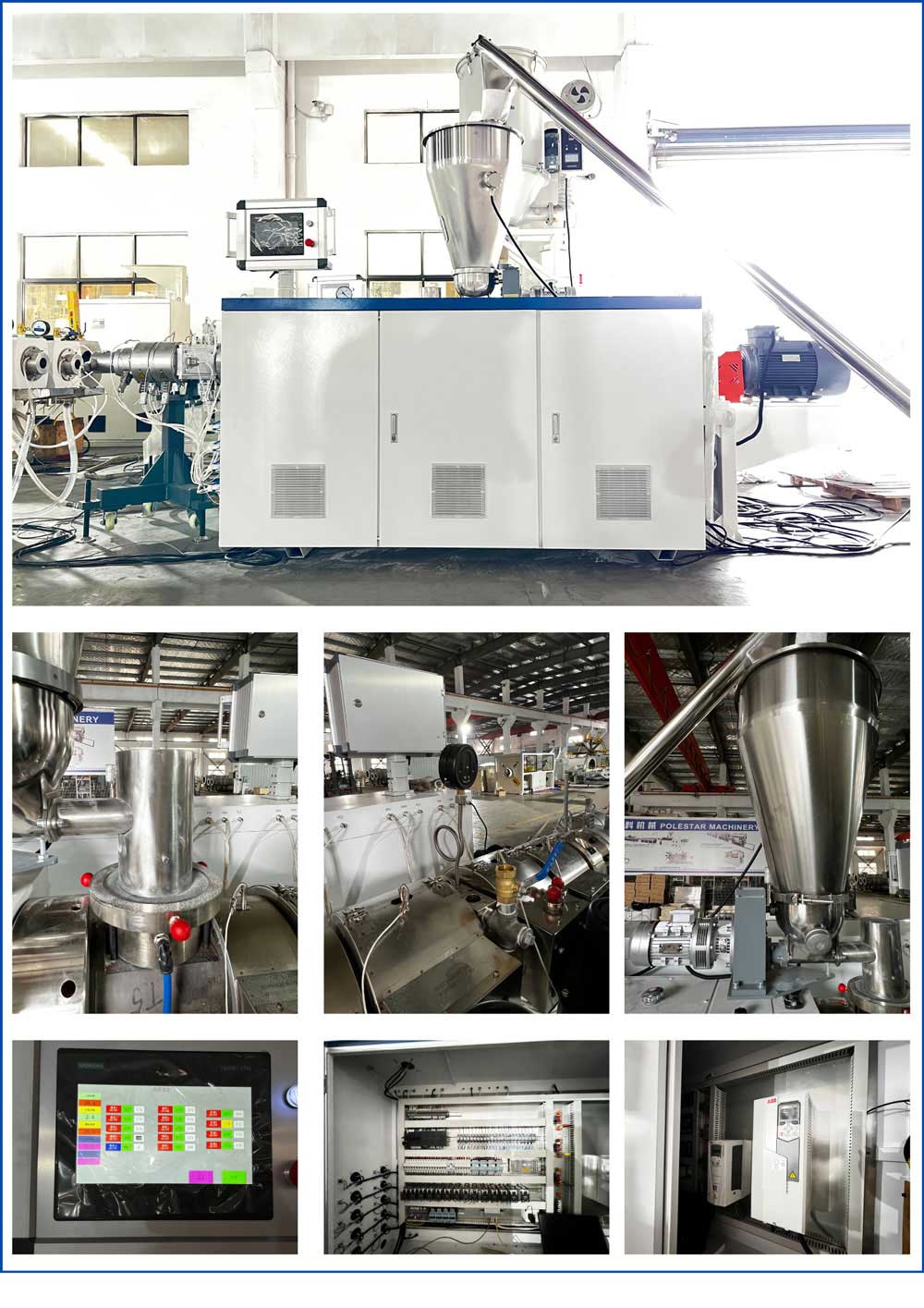
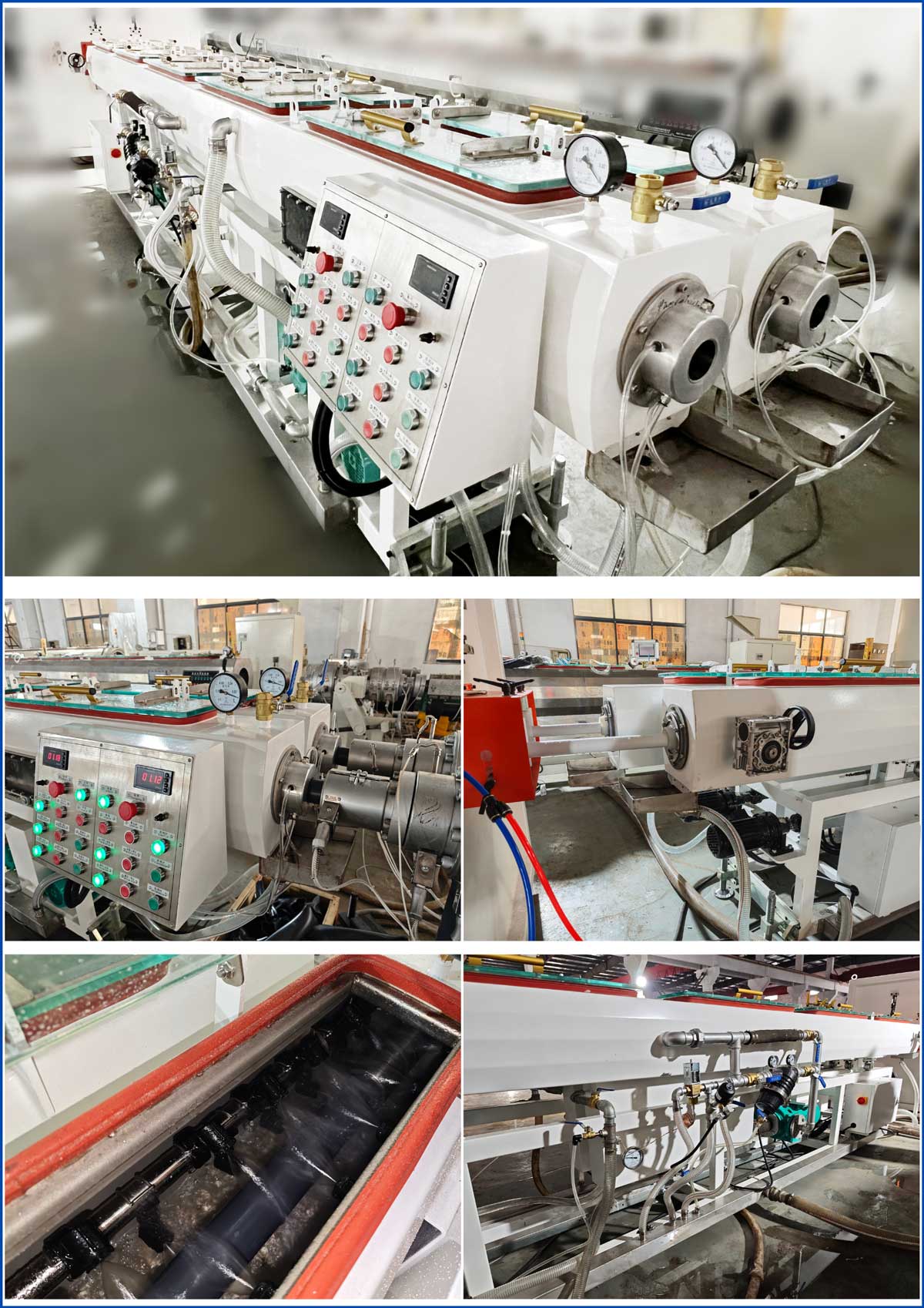
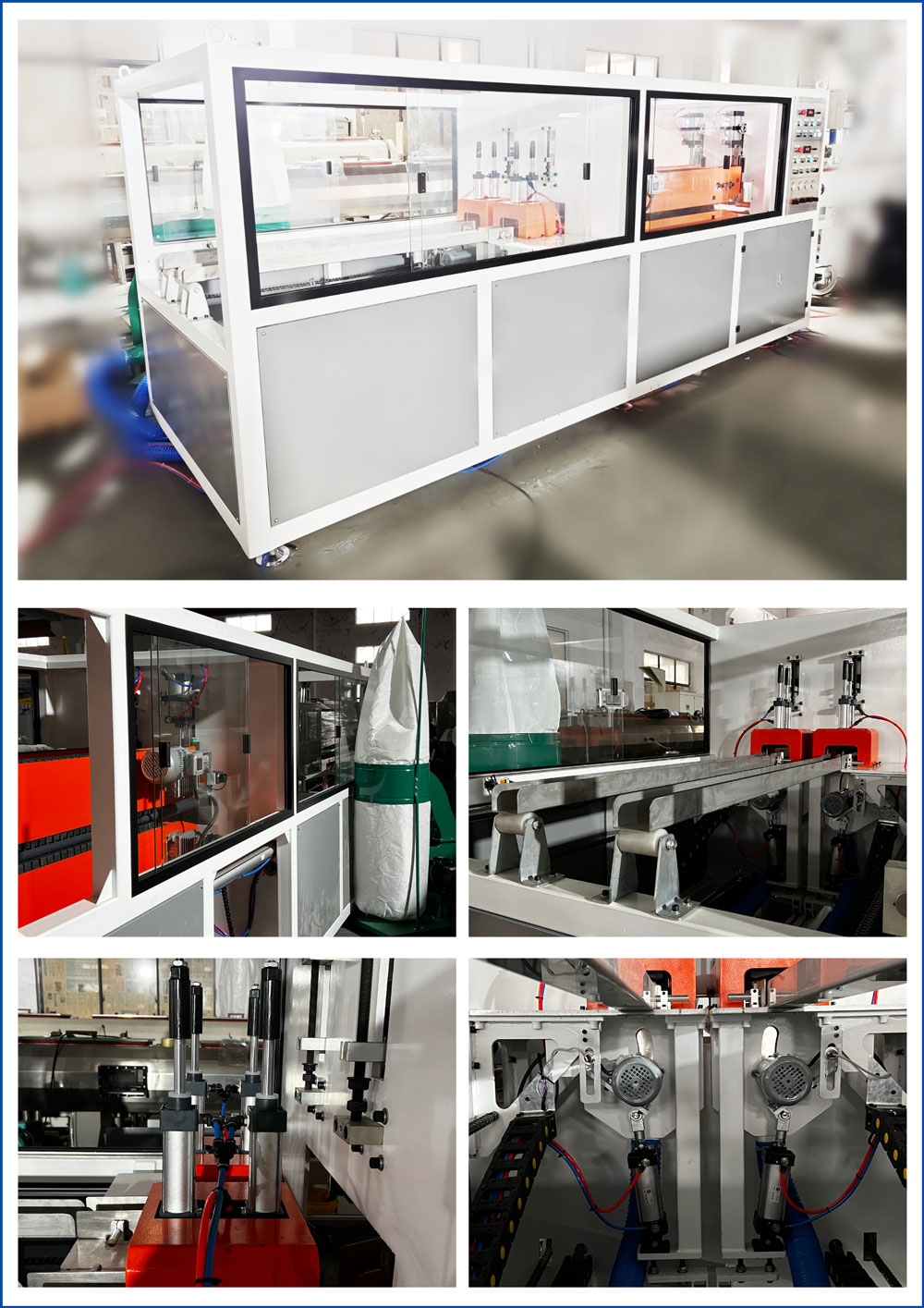
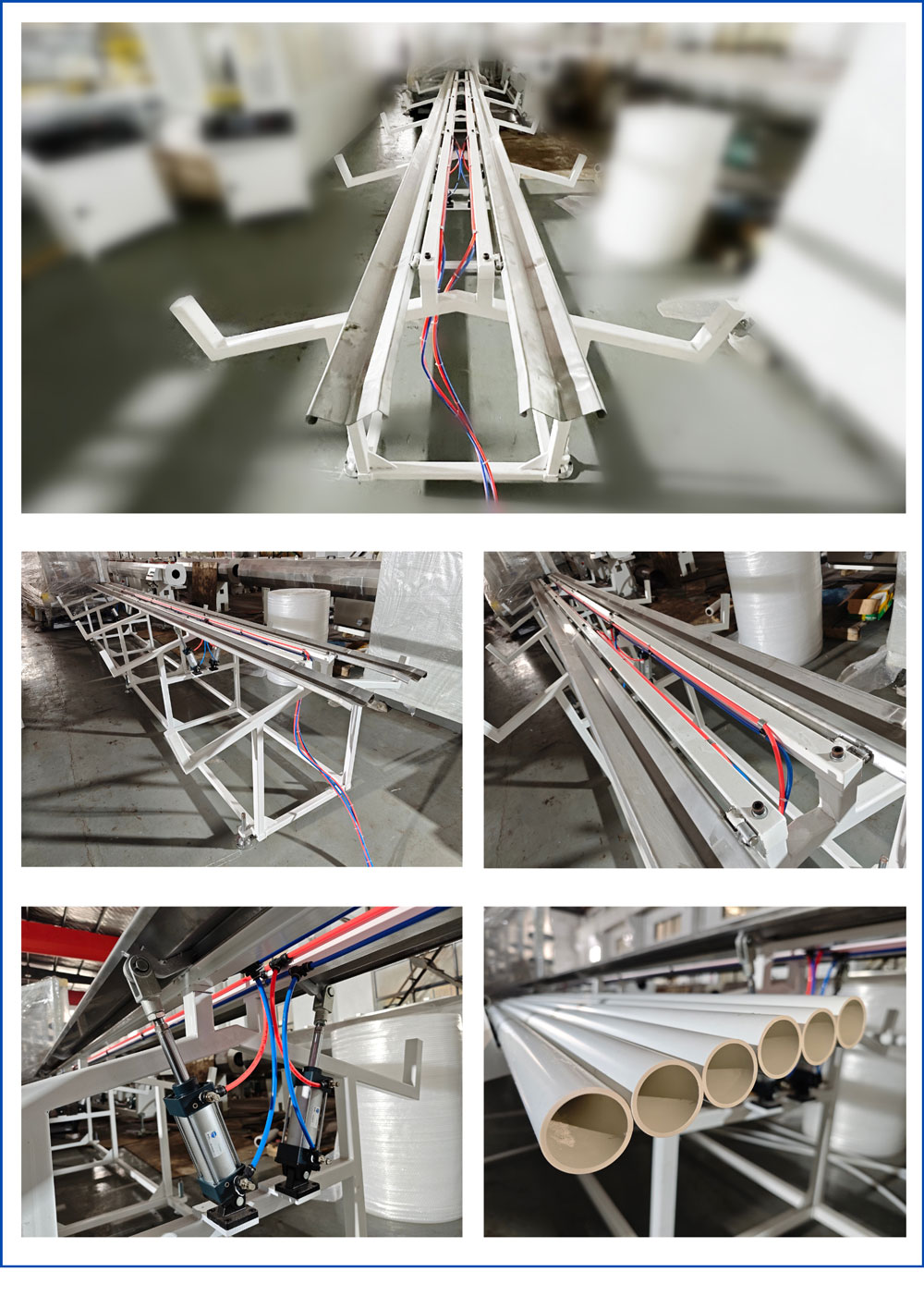
Applications
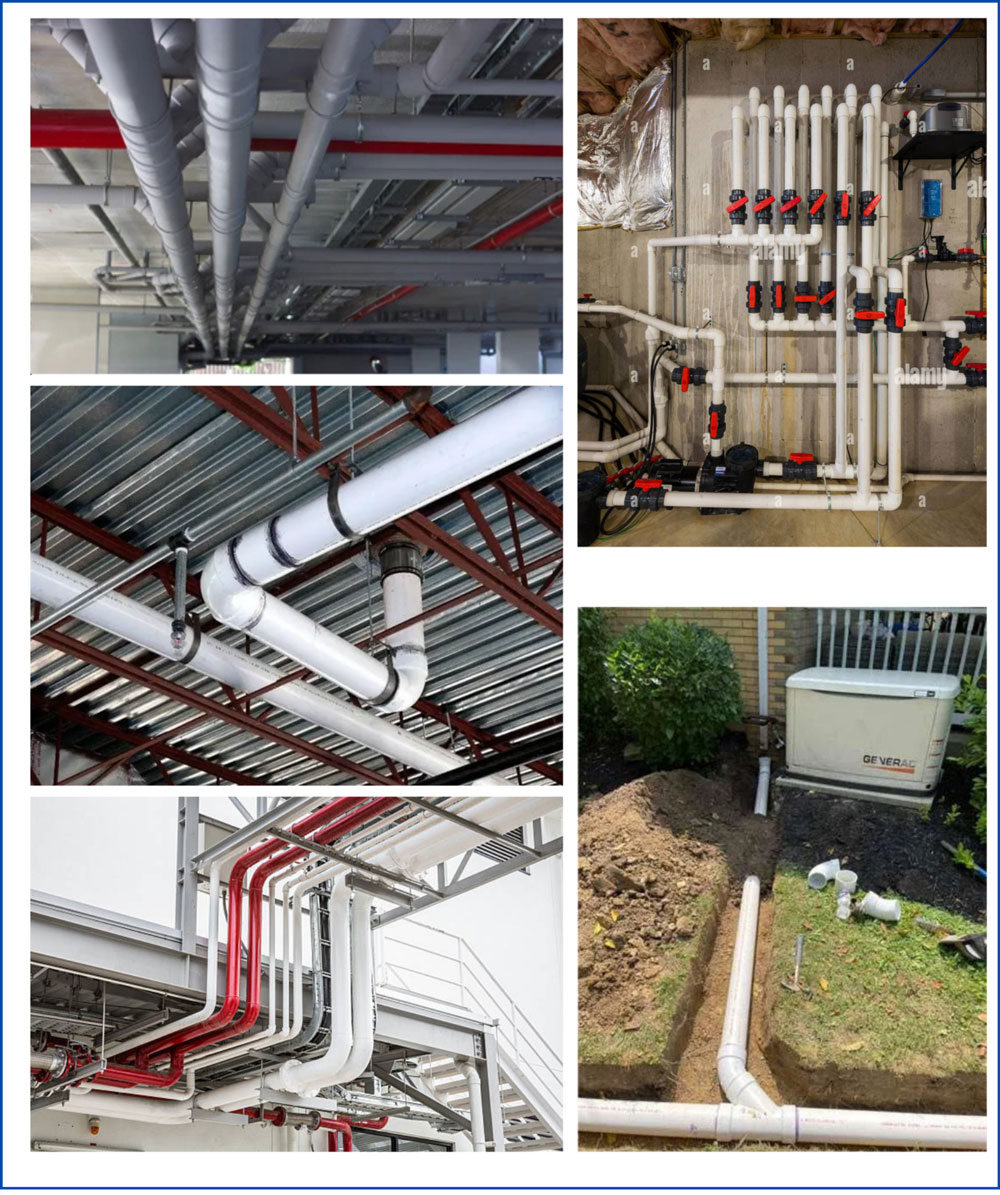