Main Function and Description
The vacuum calibration tank is typically constructed from durable materials such as stainless steel or high-grade plastic to withstand the corrosive nature of water and the pressures involved in the vacuum process. It is designed to accommodate smaller diameters, specifically for pipes ranging from 160mm to 450mm. Here’s an overview of its function and description:
1. Calibration: The primary function of the vacuum calibration tank is to ensure that the extruded plastic pipe achieves the correct dimensions. As the pipe exits the extruder, it is still hot and flexible. The tank uses vacuum pressure to hold the pipe against a calibration sleeve, shaping it to the desired diameter and wall thickness.
2. Cooling: The tank is filled with water, which cools the pipe as it passes through. This cooling process solidifies the plastic, allowing it to maintain its shape. The vacuum environment enhances cooling efficiency by lowering the boiling point of water, facilitating faster heat transfer.
3. Dimensional Control: The vacuum calibration tank ensures uniformity in the dimensions of the pipe. By applying vacuum pressure, it holds the pipe securely against the calibration sleeve, preventing any deformation during the cooling process.
4. Surface Finish: The vacuum environment helps improve the surface finish of the pipe. By minimizing air pockets and ensuring even cooling, the tank contributes to a smoother surface, which is important for both aesthetic and functional purposes.
5. Quality Assurance: The calibration tank is equipped with monitoring systems to ensure that the temperature, pressure, and dimensions of the pipe are within specified limits. This real-time monitoring helps maintain quality control throughout the production process.
Main Technical Parameters:
1. Pipe OD: 160MM, 200MM, 225MM, 250MM, 280MM, 315MM, 355MM, 400MM, 450MM
2. Tank Length: 6 Meters
3. Vacuum Pump Power: 4.0 KW*2
4. Water Pump Power: 5.5 KW*2
5. Moving Motor Power: 1.5 KW
6. Tank moving forward and backward automatically.
7. Equipped with INVERTER to reduce electrical consumption.
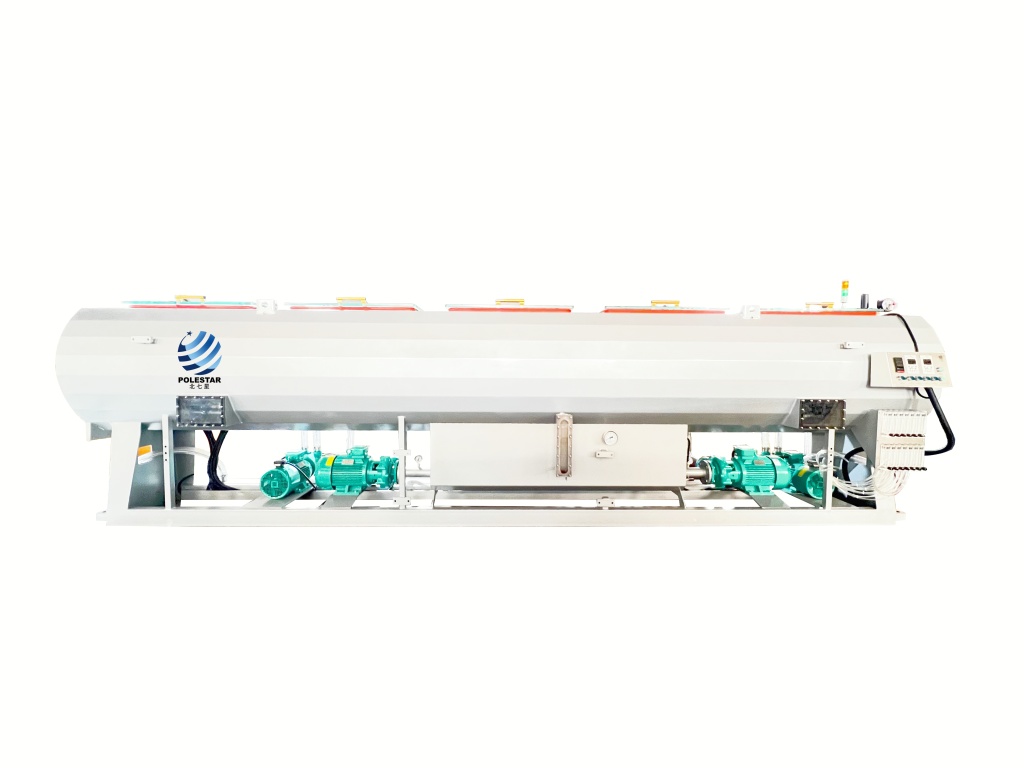
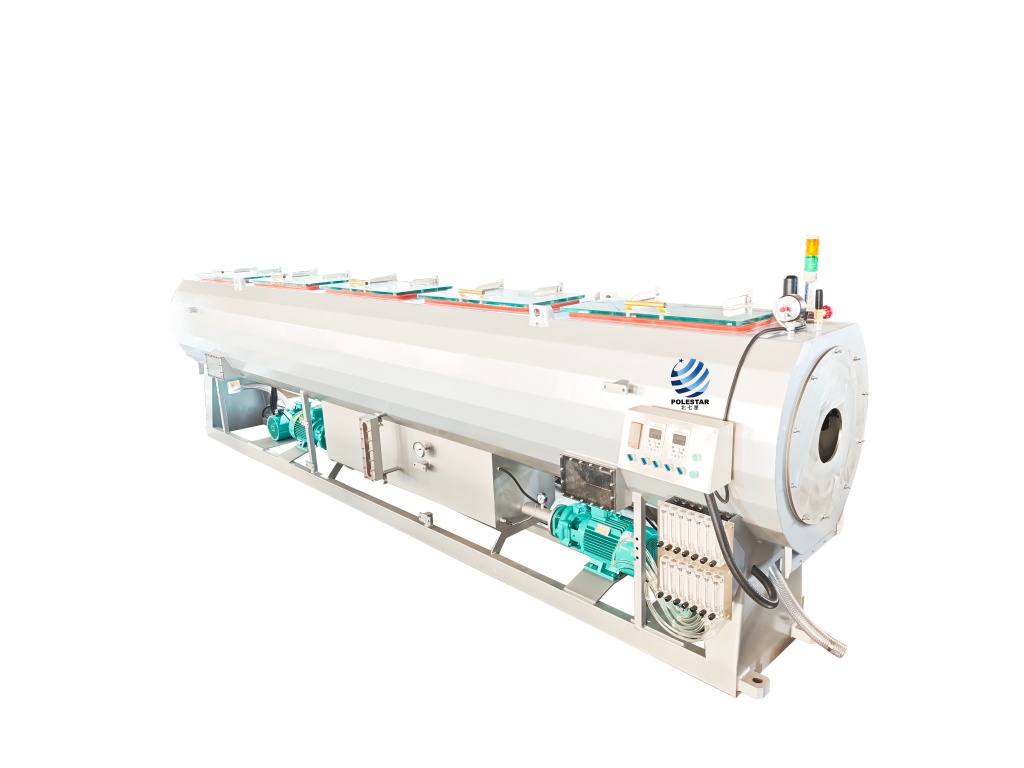
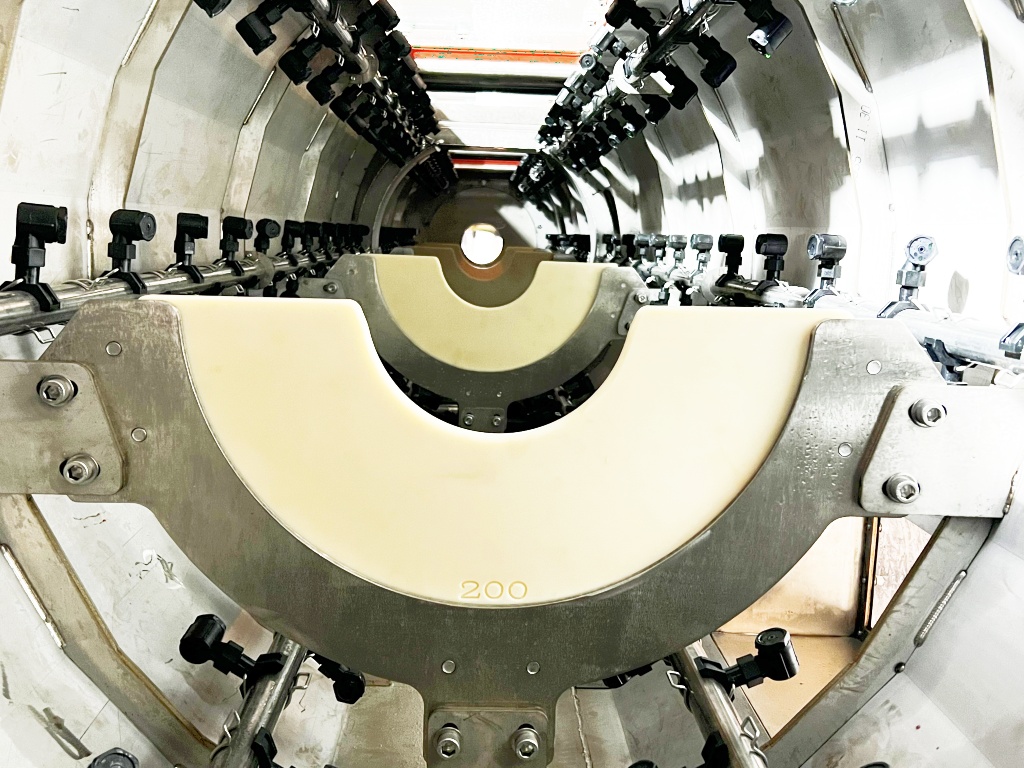
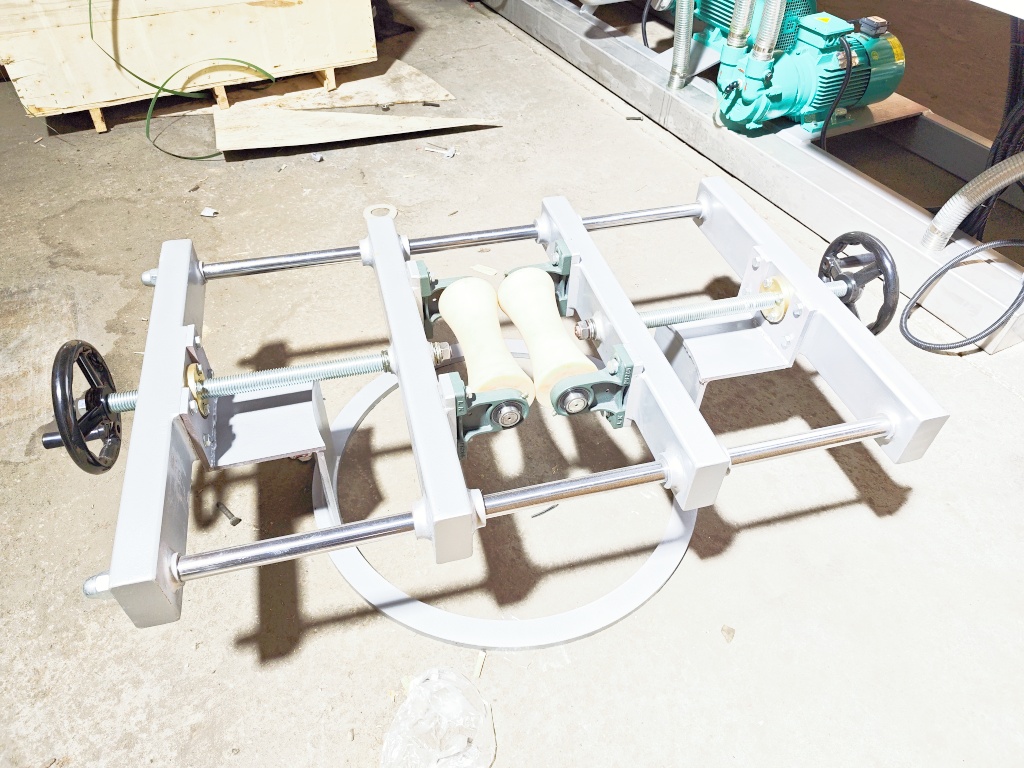
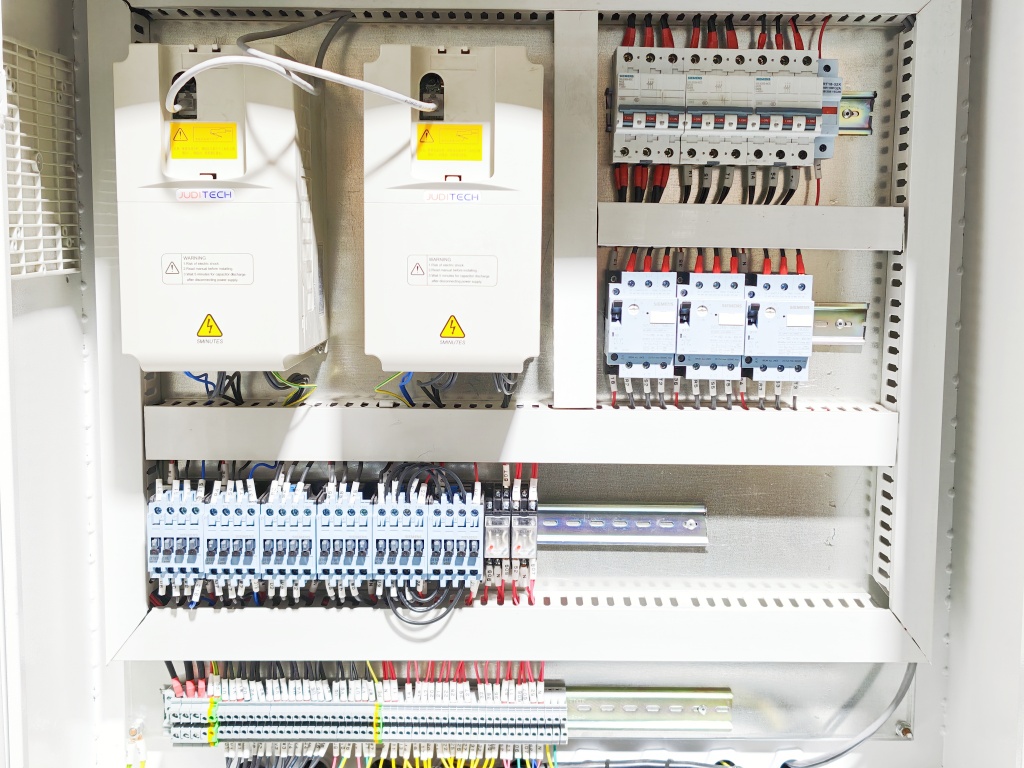
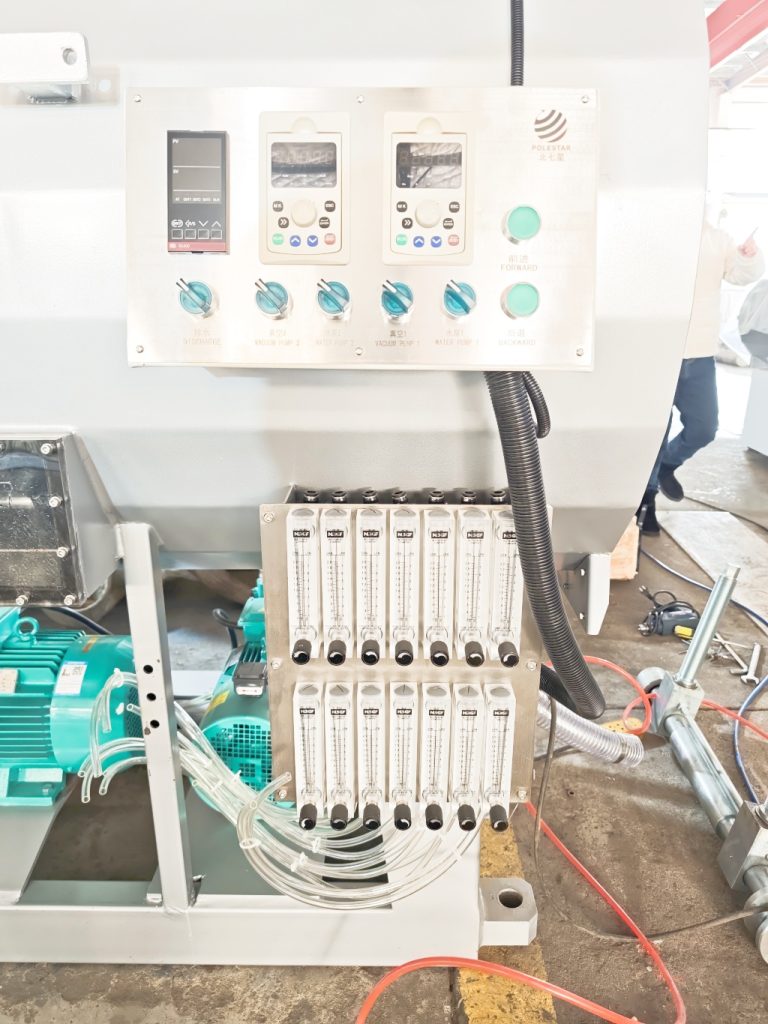